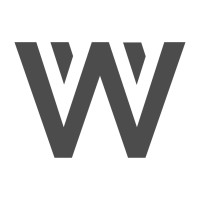
Demand Planning Manager - Kids Group
Wolverine World Wide
Wolverine Worldwide | Remote, VT, 05401
Closed - No longer accepting applications
Premium
See who posted the job
Premium
Competitive Insights
Premium
Check your commute time
Summary
The Kids Group of Wolverine Worldwide drives the design and development of childrens shoes under the companys portfolio of industry-leading brands, including Merrell, Saucony and Sperry. As experts in childrens footwear, the Kids Group team is dedicated to creating comfortable, durable and stylish shoes to take kids from first steps to the school yard. The Kids Group of Wolverine Worldwide distributes through leading retailers in the U.S. and globally in approximately 200 countries and territories.The Global Demand Planning team owns and is accountable for the global alignment from all regions for asset management, demand planning, supply planning, and fiscal alignment. This Demand Planning Manager role sits within the Kids Group of Wolverine Worldwide brand team.Current Employees interested in applying for this role, use the Current Employee tab in the top right corner to apply.Job Description
!
Inventory optimization and metrics: Manages and executes inventory asset management strategy, in units and dollars, by developing optimized inventory, turnover goals, and Open-to-Buy (OTB) targets; aligned to global goals, for assigned region and/or categories. High level of collaboration with sales and finance required.
!
Service, Margin, Quality: Manage region/category inventory flow to maximize sales and service levels, while minimize product obsolescence. Plans and manages seasonal buy programs in accordance with the buy calendar and lead times. Works to meet service level targets and reports on progress for each period. Provide recommendations to sales and finance to clear out underperforming stock.
!
On-hand SKU optimization: Manage on-hand SKU counts to established KPIs and continuously evaluates performance. Sets the branded Inventory planning classification strategy (level of on-hand inventory by SKU).
!
Forecasting: Create and validate shipment forecasts at the stock number level, utilizing brand strategy, trend, account forecasts, competitive information and market conditions. Partner with sales and finance to ensure alignment between demand planning forecasts and financial forecasts; communicate any gaps/opportunities. Manages monthly and seasonal demand and supply forecasts, planned inventory and safety stock, and reconciles with OTB.
!
SKU development and Minimum Order Quantity (MOQ) analysis: Provide guidance to the global product team for seasonal development SKU efficiency based on improving productivity per SKU. Monitor and provide recommendations for expected MOQ concerns (drop, consolidated buy, pre-buy materials, etc).
!
Execution of outbound product distribution strategy: Collaborates with sales, DTC and marketing teams to provide operational support to ensure successful launch of new product into market. Collaborates with sales to construct order booking programs to ensure timely and organized backlog. Monitors booking activity against inventory flow constraints and adjusts and communicates new availability dates accordingly. Provide critical operational support of order allocation, fill, and shipment during key fiscal deadlines, at period, quarter and year-end.
!
Inventory Procurement: Lead and manage monthly factory buys, for assigned region and categories, in alignment with Global buy calendar, to achieve financial sales and inventory goals. Negotiate best production dates to support customer demand and inventory requirements. Maintain delivery information on all open purchase orders from issuance to receipt. Manage, collaborate and communicate production shifts due to commercialization issues or sourcing changes. Continuously monitor market sell thru, inventory levels, booking, and shipping trends to direct necessary adjustments to factory purchase order dates, styles and/or sizes. Consolidates global orders per SKU to create production efficiencies.
!
Factory Capacity and Production Management: Collaborates with GOG on short- and long-range production, receipt, and inventory forecasts by stock number, and fiscal period by factory. Manages monthly production priorities per factory in accordance with Global Brand Capacity strategies, regional demand, and market availability expectations. Participate in, and drive consensus of demand and supply in monthly collaboration meetings with global planning leadership and GOG. Leads and collaborates with commercialization and sourcing operations team to ensure production output will support largest weekly volumes. Consistently monitor changes in production flow, anticipate results of these changes, and initiate appropriate adjustments when results negatively affect plans and commitments. Identify delivery issues and construct solutions. Performs duties consistent with the Companys AAP/EEO goals and policies. Performs other duties as required/assigned by manager.
Knowledge, Skills and Abilities Required
!
Bachelors degree in a related field or equivalent work experience.
!
Advanced Excel Capabilities
!
5+ years experience in planning and/or merchandising
!
Demonstrates financially astute business management with the ability to impact financial outcomes
!
Strong analytical skills
!
Highly organized and self-motivated; able to juggle multiple priorities in a fast-paced, dynamic environment, while still achieving agreed upon deadlines
!
Knowledge of inventory math, APICS certification a plus
!
Basic understanding of product lifecycle planning
!
Strong financial acumen
!
Strong problem solving and decision-making skills
!
Understanding of supply chain/factory process
!
Strong written and verbal communication skills
!
SAP experience preferred
Working Conditions
Normal office environment. Some travel may be required.
Wolverine Worldwide has a flexible, hybrid work schedule, with three days in office and two days remote.
#LI-Hybrid
Salary Minimum
$102,000.00Salary Maximum
$138,000.00
The above statements are intended to describe the general nature and level of work being performed and are not intended to be an exhaustive list of all responsibilities, duties and skills which may be required.
Wolverine Worldwide, Inc. is committed to creating a company that is as diverse as our consumers. We value the differences in one another and believe our differences make us stronger. Our diverse and inclusive corporate culture starts with the recruitment process. We are committed to being an equal opportunity employer. We aim to create equal opportunities for our associates, customers, and suppliers regardless of race, color, religion, sex, national origin, age, disability, sexual orientation, gender identity, or any other legally protected characteristic. | #LI-DNI
The Kids Group of Wolverine Worldwide drives the design and development of childrens shoes under the companys portfolio of industry-leading brands, including Merrell, Saucony and Sperry. As experts in childrens footwear, the Kids Group team is dedicated to creating comfortable, durable and stylish shoes to take kids from first steps to the school yard. The Kids Group of Wolverine Worldwide distributes through leading retailers in the U.S. and globally in approximately 200 countries and territories.The Global Demand Planning team owns and is accountable for the global alignment from all regions for asset management, demand planning, supply planning, and fiscal alignment. This Demand Planning Manager role sits within the Kids Group of Wolverine Worldwide brand team.Current Employees interested in applying for this role, use the Current Employee tab in the top right corner to apply.Job Description
!
Inventory optimization and metrics: Manages and executes inventory asset management strategy, in units and dollars, by developing optimized inventory, turnover goals, and Open-to-Buy (OTB) targets; aligned to global goals, for assigned region and/or categories. High level of collaboration with sales and finance required.
!
Service, Margin, Quality: Manage region/category inventory flow to maximize sales and service levels, while minimize product obsolescence. Plans and manages seasonal buy programs in accordance with the buy calendar and lead times. Works to meet service level targets and reports on progress for each period. Provide recommendations to sales and finance to clear out underperforming stock.
!
On-hand SKU optimization: Manage on-hand SKU counts to established KPIs and continuously evaluates performance. Sets the branded Inventory planning classification strategy (level of on-hand inventory by SKU).
!
Forecasting: Create and validate shipment forecasts at the stock number level, utilizing brand strategy, trend, account forecasts, competitive information and market conditions. Partner with sales and finance to ensure alignment between demand planning forecasts and financial forecasts; communicate any gaps/opportunities. Manages monthly and seasonal demand and supply forecasts, planned inventory and safety stock, and reconciles with OTB.
!
SKU development and Minimum Order Quantity (MOQ) analysis: Provide guidance to the global product team for seasonal development SKU efficiency based on improving productivity per SKU. Monitor and provide recommendations for expected MOQ concerns (drop, consolidated buy, pre-buy materials, etc).
!
Execution of outbound product distribution strategy: Collaborates with sales, DTC and marketing teams to provide operational support to ensure successful launch of new product into market. Collaborates with sales to construct order booking programs to ensure timely and organized backlog. Monitors booking activity against inventory flow constraints and adjusts and communicates new availability dates accordingly. Provide critical operational support of order allocation, fill, and shipment during key fiscal deadlines, at period, quarter and year-end.
!
Inventory Procurement: Lead and manage monthly factory buys, for assigned region and categories, in alignment with Global buy calendar, to achieve financial sales and inventory goals. Negotiate best production dates to support customer demand and inventory requirements. Maintain delivery information on all open purchase orders from issuance to receipt. Manage, collaborate and communicate production shifts due to commercialization issues or sourcing changes. Continuously monitor market sell thru, inventory levels, booking, and shipping trends to direct necessary adjustments to factory purchase order dates, styles and/or sizes. Consolidates global orders per SKU to create production efficiencies.
!
Factory Capacity and Production Management: Collaborates with GOG on short- and long-range production, receipt, and inventory forecasts by stock number, and fiscal period by factory. Manages monthly production priorities per factory in accordance with Global Brand Capacity strategies, regional demand, and market availability expectations. Participate in, and drive consensus of demand and supply in monthly collaboration meetings with global planning leadership and GOG. Leads and collaborates with commercialization and sourcing operations team to ensure production output will support largest weekly volumes. Consistently monitor changes in production flow, anticipate results of these changes, and initiate appropriate adjustments when results negatively affect plans and commitments. Identify delivery issues and construct solutions. Performs duties consistent with the Companys AAP/EEO goals and policies. Performs other duties as required/assigned by manager.
Knowledge, Skills and Abilities Required
!
Bachelors degree in a related field or equivalent work experience.
!
Advanced Excel Capabilities
!
5+ years experience in planning and/or merchandising
!
Demonstrates financially astute business management with the ability to impact financial outcomes
!
Strong analytical skills
!
Highly organized and self-motivated; able to juggle multiple priorities in a fast-paced, dynamic environment, while still achieving agreed upon deadlines
!
Knowledge of inventory math, APICS certification a plus
!
Basic understanding of product lifecycle planning
!
Strong financial acumen
!
Strong problem solving and decision-making skills
!
Understanding of supply chain/factory process
!
Strong written and verbal communication skills
!
SAP experience preferred
Working Conditions
Normal office environment. Some travel may be required.
Wolverine Worldwide has a flexible, hybrid work schedule, with three days in office and two days remote.
#LI-Hybrid
Salary Minimum
$102,000.00Salary Maximum
$138,000.00
The above statements are intended to describe the general nature and level of work being performed and are not intended to be an exhaustive list of all responsibilities, duties and skills which may be required.
Wolverine Worldwide, Inc. is committed to creating a company that is as diverse as our consumers. We value the differences in one another and believe our differences make us stronger. Our diverse and inclusive corporate culture starts with the recruitment process. We are committed to being an equal opportunity employer. We aim to create equal opportunities for our associates, customers, and suppliers regardless of race, color, religion, sex, national origin, age, disability, sexual orientation, gender identity, or any other legally protected characteristic. | #LI-DNI