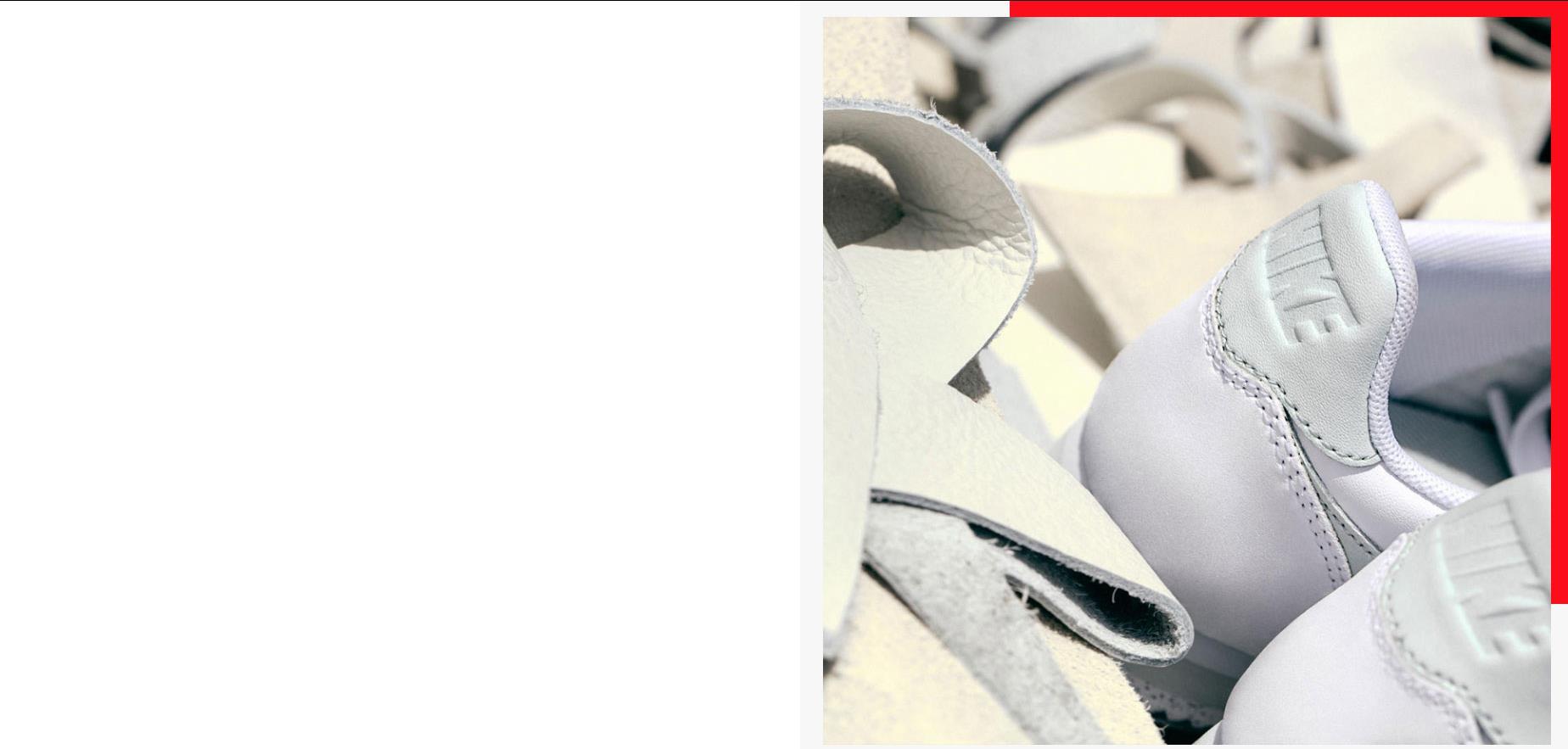
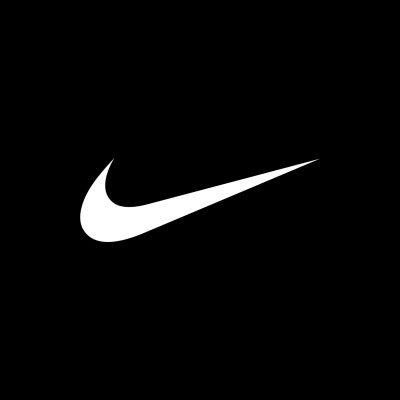
Nike Logistics Systems Manager
Nike, Inc.
Memphis, Tennessee, United States, VT, 05401
Closed - No longer accepting applications
Premium
See who posted the job
Premium
Competitive Insights
Premium
Check your commute time
Facility-North American Logistics Campus-3100 Frayser Blvd, Memphis, TN 38128
Shift- Saturday, Sunday, Monday, Tuesday- 2:30PM-12:30AM
WHO WE ARE LOOKING FOR:
As our NLS Manager, you will be part of our diverse and passionate Nike Logistics System (NLS) team supporting various functions in implementing and using our Nike Logistic System to reach our goals for the North America Logistics Team.
WHAT YOU WILL WORK ON:
Support the NLS Director in creating the NLS strategy for the distribution centers and implement resulting actions (Kaizen/Improvement projects)
Lead cross functional Kaizen teams across different shifts in improving their operation using our NLS guiding principles & culture, including various LEAN tools, techniques, and continuous improvement philosophy.
Create understanding of the end-to-end value stream(Shikumi)
Act as a coach for teams regarding the NLS principles and system.
Drive teams to identify types of wastes and non-value added activities, and how to eliminate these using root cause analysis and NLS principles.
Facilitate the implementation of the identified solutions.
Facilitate discussions to drive clarity and understanding among the cross functional members of the team and management when needed
Ensure the work is executed in a timely manner
Develop and provide training to distribution center directors, managers and employees across 4 shifts to instill an in depth understanding of the NLS culture & methodology (not just on how to use the various LEAN tools), as well as help with transition management and problem solving
Work with the various teams on defining and maintaining standards based on simulations and observations
Support NLS Director in identifying areas for improvement and setting priorities by providing relevant data driven analysis on distribution center performance and processes
Support the NLS and improvement teams in driving a culture of continuous improvement
Work with the team in fostering collaboration, alignment, and integrated execution across different functions in a matrix organization
Document, standardize and apply NLS tools and techniques, improve them where possible.
Lead a small team of NLS advisors; provide clear expectations, coach and support them in delivering high quality results
Serve as liaison with global NLS team
WHAT YOU WILL BRING:
Bachelor's degree or higher or equivalent combination of education and experience
6+ years of experience with Lean/Toyota Production System, additional Quality System experience is a plus.
3-5 years of operational warehouse experience, preferably in a leadership capacity.
Proven experience with using and implementing Lean tools and processes onto the work floor (Kaizen Events, VSM, 5S, Layered Audits, Standard Work)
System thinker. Sees the organization as an interlinked network of processes. Understands how changes to one will impact the others.
Well versed in problem solving (PCSAM, 5Whys, Fishbone diagram)
Good analytical and statistical skills preferred
Good project management skills
Experience in teaching & coaching LEAN tools a plus
Demonstrated leadership skills, including ability to influence stakeholders from various backgrounds and management levels in a matrix organization
Comfortable with change, able to tackle new priorities efficiently
Service oriented, tries to get a solution designed around the customer
Able to effectively communicate with stakeholders from various backgrounds/functions using a wide range of communication methods
Willingness and ability to come in off-shift on occasion when a project requires
Excellent command of Microsoft Office (PowerPoint, Excel, Word, Visio, SharePoint), knowledge of Manhattans WM a plus
Flexibility in future to move to a different shift or location primarily in mid-south network based on business needs.