Derek Egbert: Experienced Leader in Continuous Improvement and Program Management Seeking Next New Adventure | PMP | Six Sigma Black Belt in Denver Metropolitan Area, TX
Derek Egbert
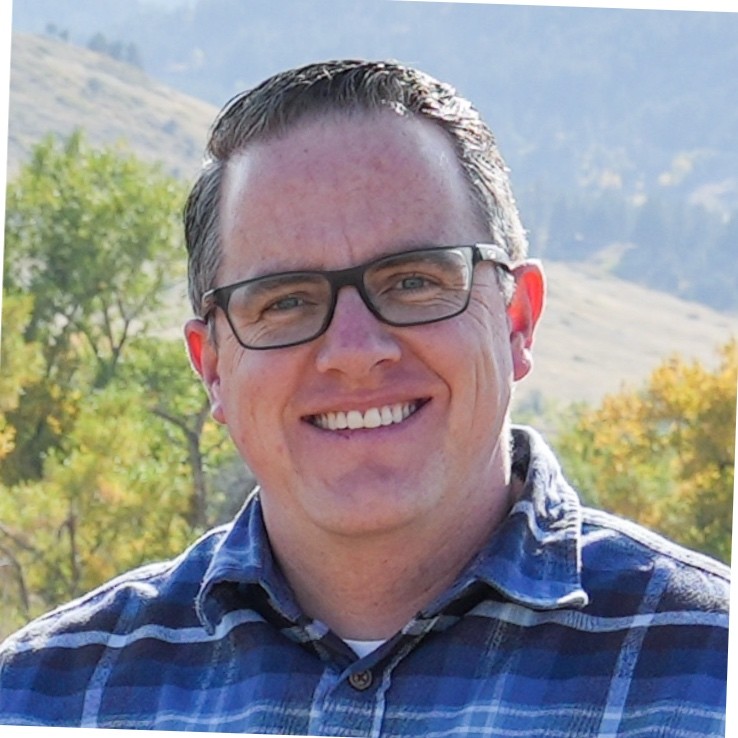
Experienced Leader in Continuous Improvement and Program Management Seeking Next New Adventure | PMP | Six Sigma Black Belt
Denver Metropolitan Area | US
Interests
No information
Industries
Bike
Moto & Powersports
Outdoor
Work experience
Safari AI
Advisor | 01/2025 - Current
Advisor to video-based AI technology company that helps businesses monitor, track, and improve their physical operations in new and innovative ways. Safari AI works with clients across theme parks, sporting venues, retail, F&B, and more. Current focus of advisory support is providing operational insights to help drive effective scope for clients.
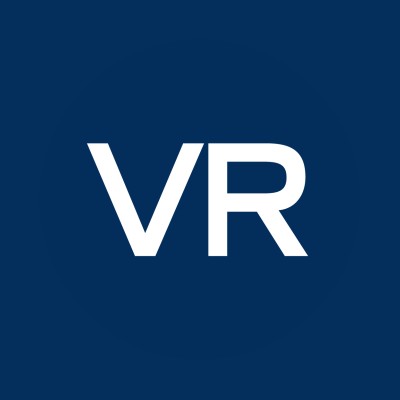
Vail Resorts
Vice President Operational Insights | 10/2023 - 01/2025
Enterprise program lead for rollout of Workforce Management Program across mountain resorts, retail outlets, and hospitality locations across North America with goal of improving budgeting, staffing, and scheduling processes. Led cross-functional teams in program design, configuration activities, and ongoing support and provided regular executive leader updates. First year labor savings of $9.6M vs target of $8.1M driven by improved budgeting and labor management capabilities. Drove labor standards budgeting process for 24/25 season and captured $5M/yr in incremental labor savings.
Designed strategy and supported rollout of new parking reservation program for two Lake Tahoe resorts with history of chronic peak-day traffic backups. Following launch, both resorts saw dramatic improvements to traffic flow on peak days. Efforts at Northstar drove 80% reduction of significant highway backups in first year and resort broke single-day skier visitation records multiple times due to capacity unlock from increased carpooling.
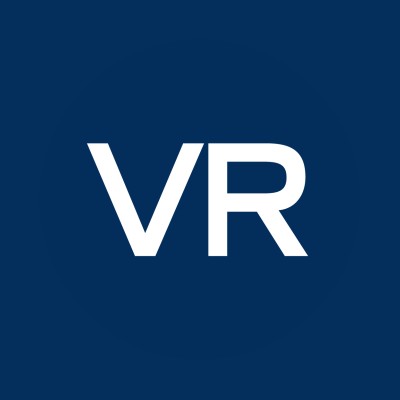
Vail Resorts
Senior Director of Operational Insights | 10/2021 - 10/2023
Enabled data-driven decision-making capabilities in lift operations, lift maintenance, and parking operations by leading creation of Ops Insights team. Led cross-functional efforts to create data-collection tools, performance metrics, and dashboards supporting operations leaders. Insights around lift ridership, wait times, and skier behaviors were used in guiding operations and supported planning of over $100M of capital for new lift projects.
Leveraged input from key leaders and conducted in-field studies to optimize lift loading/unloading standards. Efforts across multiple seasons drove a 6% increase in lift loading performance, combined capacity improvements equivalent to ~$36M in new lift investment and contributed to 30% reduction of 10+ minute waits in lift lines. Guest satisfaction scores for Lift Experience improved YoY following launch of program.
The Walt Disney Company
Project Manager, Industrial Engineering | 06/2021 - 10/2021
Optimized daily opening procedures for new Star Wars ride, shaving two hours off of daily checklist process by leveraging Six Sigma tools to clearly identify process opportunities and solutions. Saved $200k/yr in labor and gave back two hours per day of attraction availability to split across guest operations and maintenance activities.
Launched new work order submission and tracking program across entire Disneyland Resort to streamline and simplify maintenance work order request process. New process reduced call center labor needs and improved communication flow with operational groups and is still being used at the resort.
The Walt Disney Company
Senior Industrial Engineer | 12/2017 - 06/2021
Coordinated field studies and Gantt charting to reduce time window needed to complete opening checklists at four popular rides. Shortened pre-opening work window at each attraction by 30 minutes with labor savings around $100k/yr and provided maintenance teams more cushion to support on-time openings.
Drove $500k/yr in labor savings by identifying complex overtime practices and patterns across resort maintenance teams and by providing leaders with better tools to manage overtime. Recommended policy changes to senior leaders that were quickly adopted and curbed unapproved overtime costs.
Conducted overnight custodial in-field studies and identified supply chain improvement opportunity. Designed and implemented vendor managed inventory (VMI) solution and reduced frequency of purchase orders per year by 98%, reduced frequency of goods receipts by 50%, and supported a capital cost avoidance of $500K.
Mars Wrigley Confectionery
Industrial Engineer | 07/2014 - 11/2017
Led North American Master Planning process across five key manufacturing sites that drafted future facility layouts and capital plans for over $1B in future investments. This process required significant cross-functional coordination, leadership, and organization to drive pre-work and on-site event coordination.
Enabled future growth of the $500M+/yr TWIX® brand in North America by building five-year supply chain capacity and sourcing plans, scoping investments, writing capital project proposals, and by coordinating planning activities across Marketing, Sales, R&D, and Engineering teams.
Mars Wrigley Confectionery
Central Engineering Training and Recruiting Manager | 07/2012 - 07/2014
Recruited and onboarded 30 new full-time engineers to support delivery of yearly $200M+ capital projects budget. Led engineering internship program including recruiting, managing scope of work, and FT offer process.
Mars Wrigley Confectionery
Associate Controls Project Engineer | 06/2010 - 07/2012
Led $4M+ in capital projects for DOVE®, 3 MUSKETEERS®, MILKY WAY® and M&M'S® brands in areas of controls and process engineering, delivered projects on-time and within budget.
Continental Airlines
MBA Student Consultant | 08/2009 - 12/2009
Developed a new preventative maintenance program for airport operations division, initiative had estimated NPV of $20M and was approved by SVP of Continental Airlines.
The Boeing Company
Lean Enterprise Intern | 05/2007 - 08/2007
Assisted in facilitating value-stream mapping classes at the Boeing C-17 factory, built teaching toolkits for instructors of lean enterprise courses.
Topcon Positioning Systems
Lean Manufacturing Intern | 05/2006 - 08/2006
Learned from lean manufacturing experts from USA and Japan. Helped redesign production floor and built workstations to enable kanban inventory management and single-piece flow.
Lawrence Livermore National Laboratory
Instructional Design Assistant | 01/1999 - 01/2001
Supported radiation and safety training program coursework development with graphic and video production. Selected to have lunch with Edward Teller, one of the directors of the historic Manhattan Project.