Khairuddin Abdul Kudus: in Ampang, 10
Khairuddin Abdul Kudus
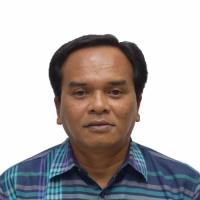
Ampang | MY
Skills
No information
Interests
No information
Industries
No information
Work experience
Sinaran Vietnam Co., Ltd
General Manager | 02/2013 - 12/2018
Reason of leaving: End of contract and looking for new challenge.
Business nature:
• Candle Manufacture for Japan and USA market.
Main Responsibilities:
• Overall control of company operation that consist Production, Quality Control, Maintenance, Warehouse,
Process Engineering, Production Control, IT, Purchasing, Shipping, Finance, Human Resource, Sales and R&D.
• Prepare and monitor company yearly budget and cost control.
• Prepare and execute the annual business plan.
• Monitoring and Controlling company Profit and Loss (P&L) condition.
• Monitoring monthly/yearly Sales forecast and achievement.
Achievement:
• Promoted to General Manager on September 2016.
• Quality: Reject reduce from 4.72% (Year 2013) to 2.33% (based on November 2018 data)
• Manpower: Manpower reduction from 943 persons to 568 persons (based on November 2018 data)
• Company Financial:
Managed to improve the company P&L
- Year 2015: Losses (10.18%)
- Year 2016: Profit 5.35%
- Year 2017: Profit 2.32%
- Year 2018 (Data from April ~ November): Profit 3.35%
• Company cashflow:
Managed to improve the company cashflow.
- Fiscal Year 2015 (April ~ March): USD 578,606.
- Fiscal Year 2016 (April ~ March): USD 1,132,923.
- Fiscal Year 2017 (April ~ March): USD 1,461,915.
- Fiscal Year 2018 (April ~ November): USD 2,397,865.
Tools used:
• Improved productivity to 98% through "Develop Human before Develop Product" concept.
• Kaizen activities - Eliminate process waste and increase productivity without compromising the quality.
• Used root cause analysis to identify the staff individual skill and capabilities.
• Lean management concept - reduce organization layers, by giving chances for staff to manage their own area so that they fell needed by the company.
• Management operating system by re-allocation staff job function to identify "right person at the right place" concept.
• Monthly KPI (Key Performance Index) monitoring.
KMS Engineering & Services Sdn. Bhd
Business Development Manager | 01/2009 - 02/2013
Date joined: January 2009 to February 2013.
Reason of leaving: Company business not doing well.
Business nature:
• Engineering - Machining (CNC Milling & Lathe) & Welding.
• Electronics - Circuit Design and PCB assembly.
• Services - Oil palm plantation maintenance, parts trading for oil & gas sectors and others.
Main Responsibilities:
• Marketing, delivery and quality control
SONY EMCS (Malaysia) Sdn. Bhd
Manager - Head of Auto Mount Department | 10/2005 - 12/2008
Date joined: October 2005 to December 2008.
Reason of leaving: Voluntary Separation Scheme (VSS).
Main Responsibilities:
• Operation control of the department that consist Production, Quality, Maintenance, Industrial Engineering, Process Engineering, Planning and Program.
• Prepare and monitor yearly department budget and cost control
• Prepare and execute the annual business plan
Achievements:
• Cost controls i.e. 20% manpower reduction.
• Best cost per shot for 3 conservative months in total SONY COPERATION GROUP.
• Best department award for total achievement such 5S and KAIZEN.
• Achieved single ppm (part per million) in quality.
• Improved productivity to 98% through "Develop People before Develop Product" concept.
• Monthly KPI (Key Performance Index) monitoring.
Tools used:
• Kaizen activities - Eliminate process waste and increase productivity without compromising the quality.
• Used root cause analysis to identify the staff individual skill and capabilities.
• Lean management concept - reduce organization layers, by giving chances for staff to manage their own area so that they fell needed by the company.
• Management operating system by re-allocation staff job function to identify "right person at the right place" concept.
Intro-Frontier Electronic Sdn. Bhd
Factory Manager | 10/2002 - 03/2005
Reason of leaving: Company ceased operation.
Business nature:
• Injection Moulding, Spraying Process, Laser Cut Process for Car Audio Panel for Mazda, Ford etc.
Main Responsibilities:
• Operation control of the department that consist Production, Quality Control, Maintenance, Process Engineering, Planning, Purchasing and Store.
• Prepare and monitor yearly department budget and cost control
Achievements:
• Cost controls i.e. 50% manpower reduction.
• Improved productivity to 95% through "Develop People before Develop Product" concept.
• Reduce company losses by 70%.
• Best supplier award for 2 conservative years.
Tools used:
• Kaizen activities - Eliminate process waste and increase productivity without compromising the quality.
• Used root cause analysis to identify the staff individual skill and capabilities.
• Management operating system by re-allocate staff job function to identify "right person at the right place" concept.
• Monthly KPI (Key Performance Index) monitoring.
TAKANO Electronics (M) Sdn. Bhd
Factory Manager | 04/2000 - 04/2002
Reason of leaving: End of contract.
Business nature:
• Injection Moulding, Printing Process and Assembly Process for Car Audio Panel.
Main Responsibilities:
• Operation control of the department that consist Production, Quality Control, Maintenance, Engineering, Planning, Warehouse and Store.
• Plan and monitoring the new model progress from initial stage until mass production.
• Prepare and monitor yearly department budget and cost control
Achievements:
• Cost controls i.e. 50% manpower reduction.
• Improved productivity to 93% through "Develop People before Develop Product" concept.
• Improve company profit by 20%.
• Best supplier award.
Tools used:
• Kaizen activities - Eliminate process waste and increase productivity without compromising the quality.
• Used root cause analysis to identify the staff individual skill and capabilities.
• Management operating system by re-allocate staff job function to identify "right person at the right place" concept.
• Monthly KPI (Key Performance Index) monitoring.
Kenwood Electronics Technology Malaysia Sdn. Bhd
IQC & SQE Department Manager | 02/1998 - 04/2000
Date joined: February 1998 to April 2000.
Reason of leaving: Transferred to Takano Electronics (Kenwood's developed supplier) to improve quality and delivery.
Main Responsibilities:
• Incoming material quality control.
• Monitoring the improvement progress of supplier in order to improve incoming materials quality.
• Working hand in hand with suppliers in improving their quality to achieve free-inspection standard.
• Prepare and monitor yearly department budget and cost control
Achievements:
• Set-up Supplier Quality Engineering (SQE) section.
• 14 suppliers achieved free-inspection standard program
Tools used:
• Kaizen activities - Eliminate process waste and increase productivity without compromising the quality.
• Used root cause analysis to identify the staff individual skill and capabilities.
• Management operating system by re-allocate staff job function to identify "right person at the right place" concept
• Improve supplier's quality through Engineering method.
• Monthly KPI (Key Performance Index) monitoring.
Panasonic System Networks Malaysia Sdn. Bhd
Department Head - Surface Mount and PCB Assembly Department | 03/1993 - 12/1997
Date joined: March 1993 to December 1997.
Main Responsibilities:
• Operation control of the department that consist Production, Quality, Maintenance, Material Control, Process Engineering, Planning and Program.
• Prepare and monitor yearly department budget and cost control.
• Control Sub-contractors Company on delivery and quality performance.
Achievements:
• Best department award.
Tools used:
• QCC activities.
• Kaizen activities - Eliminate process waste and increase productivity without compromising the quality.
• Monthly KPI (Key Performance Index) monitoring.