Jim Karpinski: in Albuquerque, NM
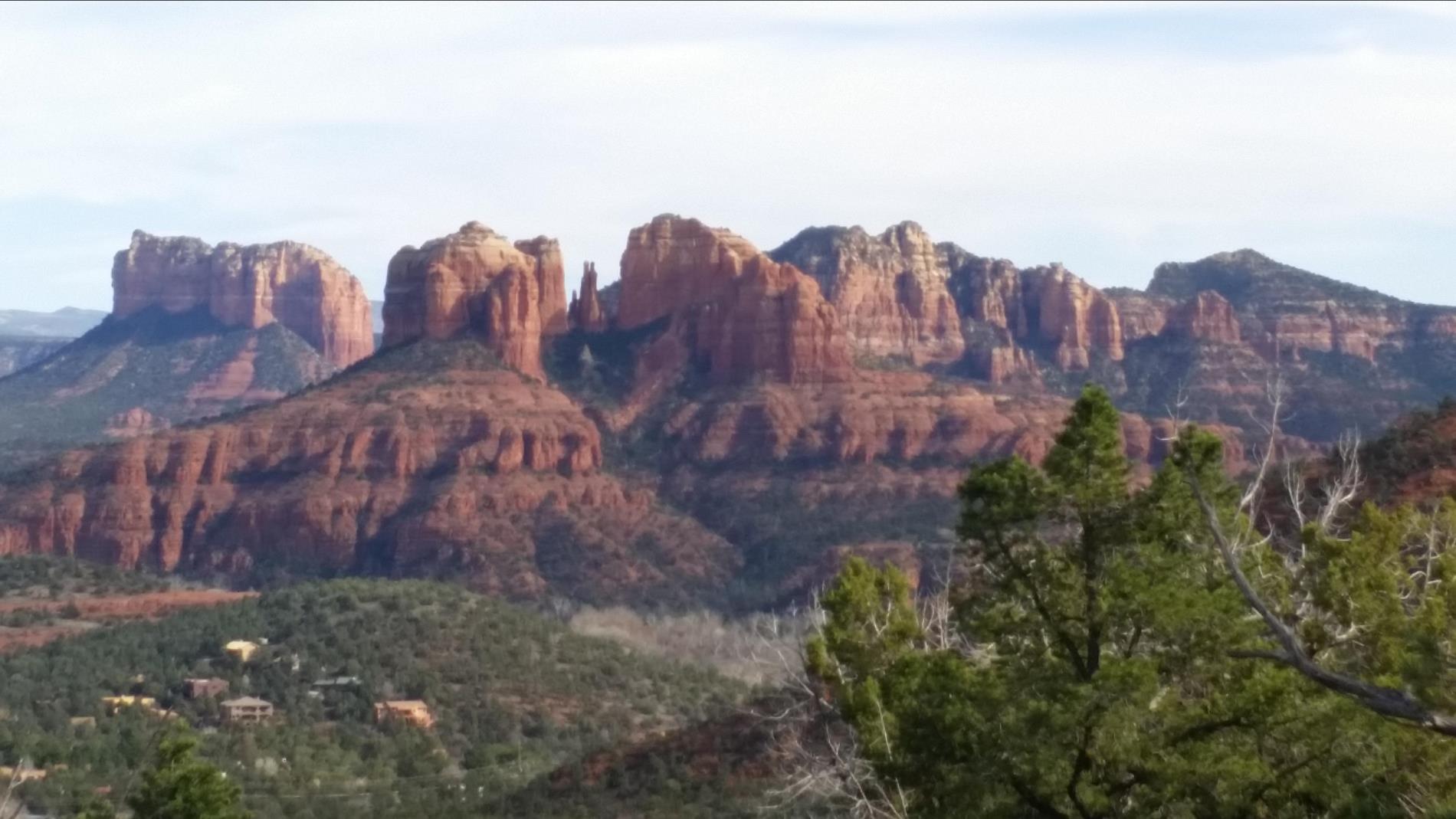
Jim Karpinski
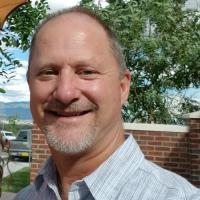
Albuquerque | United States
Skills
No information
Interests
Camping
Hiking
Fly fishing
Industries
Fishing
Outdoor
Snow
Summary
No information
Activity
Projects
No information
Work experience
Supplier to MBUSI
Lean Consultant | 12/2019 - 02/2020
• Responsible for implementing Lean Principles into current production areas.
• Organize and roll out systems to ensure quality and efficiencies meet production goals.
• Create tracking systems to monitor employee performance and attendance.
• Work with other departments to develop best practice for ensuring quality products are shipped to the customer.
• Present new ideas to management that will increase first time capability.
Formel D
Contractor to MBUSI | 06/2019 - 12/2019
Operations Supervisor
• Responsible for the Logistics area.
• Organized roll out of inventory systems to technicians. (SAP, CLS, RPM, and SharePoint).
• Set in place an organized procedure for vehicle and parts to meet at the repair bay to cut down on wait time of tech waiting on parts. This also included having an access database built to track movement of vehicle, and parts.
• Created tracking systems to monitor inventory accuracy and workforce performance for the logistics area.
• Manage daily work force for both night and day shifts.
• Work with other department to develop best practice for completing vehicle in a timely manner.
• Orchestrated move from the original repair Site to current repair site, including all parts, racking, and equipment.
Kevothermal LTD
Production Manager | 05/2017 - 06/2019
• Responsible for 60+ employees.
• Implement lean principles using MPS in the production area.
• Develop performance tracking systems.
• Coach employees from the supervisor down in lean thinking.
• Develop an intern program for time studies, bottleneck breaking, and line balancing. Implemented findings into new station layout
• Responsible for writing evaluations, coaching employees on new methods, developing standard operating procedures, and training documentation
• Strategic manpower planning for new facility. Developed a plan to ramp manpower up at new facility while maintaining full production at existing facility without adding headcount.
• Develop new organization structure for production department from the tech up to supervisor.
• Research, plan, and implement a three-shift five-day schedule model to replace a four-shift seven-day model.
• Brought production yield up from a five-year average of 85% to 94% over the course of one year
• Initiate disciplinary actions for safety. attendance, HR policy violations, and performance.
OGB Architectural Millworks
Production Manager | 04/2016 - 05/2017
• Oversee day to day operations of the production facility.
• Areas of responsibilities include safety, production, hiring, addressing HR issues, receiving, shipping, and building/equipment maintenance.
• Implement lean principles using MPS in the production area.
• Introduce new communication practices to improve inner departmental team building.
• Develop an intern program to study EHPV.
Education history
Ferris State University
Associate in Applied Science AAS
Connections
Companies (0)
No information